5S is a system for organizing spaces so work can be performed efficiently, effectively, and safely. This system focuses on putting everything where it belongs and keeping the workplace clean, which makes it easier for people to do their jobs without wasting time or risking injury.
5S Translation
The term 5S comes from five Japanese words:
- Seiri
- Seiton
- Seiso
- Seiketsu
- Shitsuke
In English, these words are often translated to:
- Sort
- Set in Order
- Shine
- Standardize
- Sustain
Each S represents one part of a five-step process that can improve the overall function of a business.
The Origins of 5S – 5S & Lean Manufacturing
5S began as part of the Toyota Production System (TPS), the manufacturing method begun by leaders at the Toyota Motor Company in the early and mid-20th century. This system, often referred to as Lean manufacturing in the West, aims to increase the value of products or services for customers. This is often accomplished by finding and eliminating waste from production processes.
Lean manufacturing involves the use of many tools such as 5S, kaizen, kanban, jidoka, heijunka, and poka-yoke. 5S is considered a foundational part of the Toyota Production System because until the workplace is in a clean, organized state, achieving consistently good results is difficult. A messy, cluttered space can lead to mistakes, slowdowns in production, and even accidents, all of which interrupt operations and negatively impact a company.
By having a systematically organized facility, a company increases the likelihood that production will occur exactly as it should.
Benefits of 5S
Over time, the 5S methodology leads to many benefits, including:
- Reduced costs
- Higher quality
- Increased productivity
- Greater employee satisfaction
- A safer work environment
What Are the 5 S's?
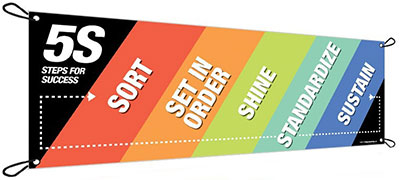
The 5S concept might sound a little abstract at this point, but in reality, it's a very practical, hands-on tool that everyone in the workplace can be a part of.
5S involves assessing everything present in a space, removing what's unnecessary, organizing things logically, performing housekeeping tasks, and keeping this cycle going. Organize, clean, repeat.
Let's take a closer look at each of the parts of 5S.
Sort
The first step of 5S, Sort, involves going through all the tools, furniture, materials, equipment, etc. in a work area to determine what needs to be present and what can be removed. Some questions to ask during this phase include:
- What is the purpose of this item?
- When was this item last used?
- How frequently is it used?
- Who uses it?
- Does it need to be here?
These questions help determine the value of each item. A workspace might be better off without unnecessary items or items used infrequently. These things can get in the way or take up space.
Keep in mind the best people to assess the items in space are the people who work in that space. They are the ones who can answer the above questions.
When a group has determined that some items aren't necessary, consider the following options:
- Give the items to a different department
- Recycle/throw away/sell the items
- Put items into storage
For cases when an item's value is uncertain — for example, a tool hasn't been used recently, but someone thinks it might be needed in the future — use the red tag method. Red tags are usually cardboard tags or stickers that can be attached to the items in question. Users fill out the information about the item such as
- Location
- Description
- Name of person applying the tag
- Date of application
Then the item is placed in a "red tag area" with other questionable items. If after a designated amount of time (perhaps a month or two) the item hasn't been used, it's time to remove it from the workspace. It's not worth hanging onto things that never get used since they just take up space.
Tip: Set a reminder—on your phone or computer, or posted somewhere in the workspace—to check back in with the red tag area so it doesn't get forgotten.
Set in Order
Once the extra clutter is gone, it's easier to see what's what. Now work groups can come up with their strategies for sorting through the remaining items. Things to consider:
- Which people (or workstations) use which items?
- When are items used?
- Which items are used most frequently?
- Should items be grouped by type?
- Where would it be most logical to place items?
- Would some placements be more ergonomic for workers than others?
- Would some placements cut down on unnecessary motion?
- Are more storage containers necessary to keep things organized?
During this phase, everyone should determine what arrangements are most logical. That will require thinking through tasks, the frequency of those tasks, the paths people take through the space, etc.
Businesses may want to stop and think about the relationship between the organization and larger Lean efforts. What arrangement will cause the least amount of waste?
In Lean manufacturing, waste can take the form of:
- Defects
- Waiting time
- Extra motion
- Excess inventory
- Overproduction
- Extra processing
- Unnecessary transportation
- Unutilized talents
Tip: For 5S, specifically consider how the layout and organization of an area could increase/decrease waiting time, motion, and unnecessary transportation.
Shine
Everyone thinks they know what housekeeping is, but it's one of the easiest things to overlook, especially when work gets busy. The Shine stage of 5S focuses on cleaning up the work area, which means sweeping, mopping, dusting, wiping down surfaces, putting tools and materials away, etc.
In addition to basic cleaning, Shine also involves performing regular maintenance on equipment and machinery. Planning for maintenance ahead of time means businesses can catch problems and prevent breakdowns. That means less wasted time and no loss of profits related to work stoppages.
Shining the workplace might not sound exciting, but it's important. And it shouldn't just be left up to the janitorial staff. In 5S, everyone takes responsibility for cleaning up their workspace, ideally daily. Doing so makes people take ownership of the space, which in the long run means people will be more invested in their work and the company.
Tip: How to clean may seem obvious, but make sure people know how to properly Shine their spaces. Show employees — especially new employees — which cleaners to use, where cleaning materials are stored, and how to clean equipment, particularly if it's equipment that could be easily damaged.
Standardize
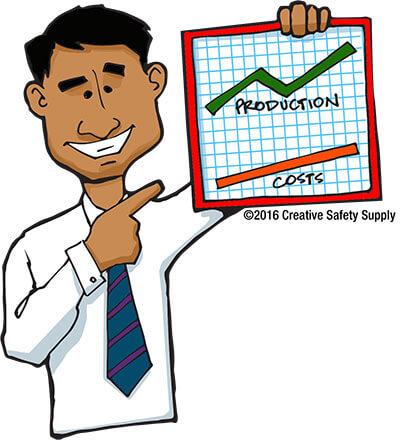
Once the first three steps of 5S are completed, things should look pretty good. All the extra stuff is gone, everything is organized, spaces are cleaned, and equipment is in good working order.
The problem is, when 5S is new at a company, it's easy to clean and get organized…and then slowly let things slide back to the way they were. Standardize makes 5S different from the typical spring-cleaning project. Standardize systematizes everything that just happened and turns one-time efforts into habits. Standardize assigns regular tasks, creates schedules, and posts instructions so these activities become routines. It makes standard operating procedures for 5S so that orderliness doesn't fall by the wayside.
Depending on the workspace, a daily 5S checklist or a chart might be useful. A posted schedule indicating how frequently certain cleaning tasks must occur and who is responsible for them is another helpful tool.
Initially, people will probably need reminders about 5S. Small amounts of time may need to be set aside daily for 5S tasks. But over time, tasks will become routine and 5S organizing and cleaning will become a part of regular work.
Tip: Visual cues such as signs, labels, posters, floor marking tape, and tool organizers also play an important role in 5S. They can provide directions and keep items in place, in many cases without words.
Sustain
Once standard procedures for 5S are in place, businesses must perform the ongoing work of maintaining those procedures and updating them as necessary. Sustain refers to the process of keeping 5S running smoothly, but also of keeping everyone in the organization involved. Managers need to participate, as do employees out on the manufacturing floor, in the warehouse, or in the office. Sustain is about making 5S a long-term program, not just an event or short-term project. Ideally, 5S becomes a part of an organization's culture. And when 5S is sustained over time, that's when businesses will start to notice continuous positive results.
Tip #1: To help sustain 5S practices, make sure all new employees (or employees who switch departments) receive training about their area's 5S procedures.
Tip #2: Keep things interesting. Look at what other companies are doing with 5S. New ideas for organization can keep things improving and keep employees engaged.
Safety – The 6th S
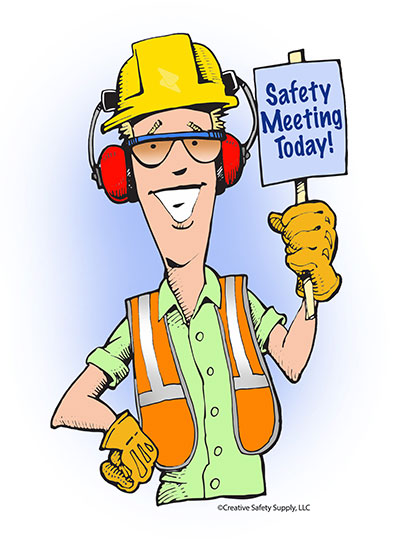
Some companies like to include a sixth S in their 5S program: Safety. When safety is included, the system is often called 6S. The Safety step involves focusing on what can be done to eliminate risks in work processes by arranging things in certain ways.
This might involve setting up workstations so they're more ergonomic, marking intersections—such as the places where forklifts and pedestrians cross paths—with signs, and labeling the storage cabinet for cleaning chemicals so people are aware of potential hazards. If the layout of the workplace or the tasks people perform are dangerous, those dangers should be reduced as much as possible. That's what the sixth S focuses on.
Some people consider safety an outcome of performing the other five S's appropriately, and as a result say a sixth S isn't necessary. They think if the workspace is properly organized and cleaned and uses helpful visual safety cues, a separate safety step is unnecessary.
Neither approach to safety is right or wrong. But however a business wants to approach safety, it should be aware that paying attention to safety is important.
Tip: If mishaps and accidents do happen, stop to consider whether a 5S improvement could have prevented it. Could less clutter, cleaner walking surfaces, or better signs and labels have made a difference?
Getting Started with 5S
Even though 5S is a fairly simple concept, beginning a new 5S program can feel daunting. It's like undertaking a big cleaning project in the garage or the basement at home; there's a lot of stuff to deal with, and getting started probably doesn't sound fun.
Start with practical steps such as deciding which departments and individuals will be involved, what training is needed, and what tools to use to facilitate the process. Determining these concrete things will help begin the process of 5S implementation.
Who Should Participate in 5S?
Here's the short answer to this question: everyone. If a department is starting 5S, managers and all other employees should be included. If anyone is left out, this could lead to confusion or to messes that people don't want to take ownership of.
It is possible that some people will play a bigger role in 5S than others, which is fine. There might be 5S coordinators who are in charge of installing and maintaining 5S labeling, keeping tracking of assigned tasks, or introducing new department members to the 5S system. These people will obviously spend a lot of time thinking about 5S compared to others. Everyone should think about 5S regularly, though. 5S might initially take place as an event, but ideally it becomes a part of daily work for everyone.
It's also important to remember that company leaders should participate in 5S, especially if 5S is a company-wide effort. When people see their superiors taking 5S seriously by participating in it, they'll be more likely to take it seriously, too.
5S Training
Anyone who will participate in 5S activities needs to receive training. This could be done in a classroom setting, with a training DVD, and/or through hands-on activities. A demonstration of how 5S could occur at a workstation might also be useful.
For employees to understand why the company is going to start using 5S and why it's important, they should be given a brief history of 5S, its parts, and its benefits.
It's quite possible that the way 5S is carried out at one organization or even one department will be different from others, so groups performing 5S for the first time may need to work out the best way to perform the steps of 5S in their spaces.
In any case, everyone should receive training when 5S is new, and then any new employees who come onboard later should receive training about 5S as well.
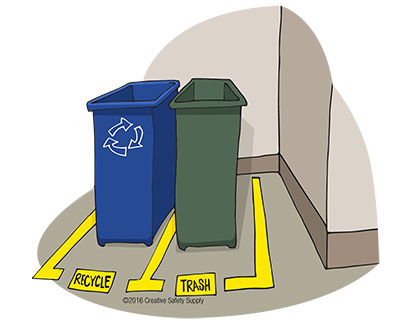
5S & Visual Communication
A key part of 5S is that it makes spaces cleaner and therefore easier to navigate. That means people can more easily get their work done. Visual communication tools such as labels, floor markings, cabinet and shelf markings, and shadow boards can make navigating spaces even simpler. Plus, these tools can help keep the workspace organized. A workplace that uses visual management in this way is often referred to as a visual workplace.
Some common visual tools used in 5S are:
- Floor Marking Tape
- These tapes can be used to outline work cells, mark the locations where equipment or materials are placed, or highlight hazards. They come in a variety of colors and patterns, and can also be used on shelves, workbenches, cabinets, and other surfaces.
- Labels and Signs
- These visuals use text, colors, and symbols to convey information. They can indicate the contents of drawers, call out hazards, or tell people where to store parts. Many styles and sizes exist, and some businesses even choose to make these in-house with a label and sign printer.
- Shadow boards & Toolbox Foam
- These visuals are helpful in workspaces with a lot of tools. Shadow boards use cutouts of tools that are placed behind the spot where a tool hangs on a pegboard. Toolbox foam works similarly, except it fits into a toolbox drawer. The tool's shape is cut out of a top layer of foam, so a bright bottom layer of foam shows through. Both of these methods highlight missing tools and tell people exactly where tools should be placed when they're finished using them.
Businesses may choose to use some or all of these visual tools. All of them help achieve the often-cited saying of 5S: “A place for everything, and everything in its place.” These tools make it clear where things belong, so clutter doesn't become a problem so easily.
Tip: If you use color-coded floor markings, tapes, or other visual cues, make sure everyone understands them. Post a color chart if necessary.
5S Outside Manufacturing – In Healthcare, the Office, or Government
5S originated in the manufacturing industry at Toyota and it has proven useful for manufacturers in many industries, not just the automobile industry. In recent decades, 5S has moved beyond manufacturing to other industries such as healthcare. Many offices also employ 5S, as do some schools and other government organizations.
The basic steps of 5S can be applied to any workplace. An office can use 5S to keep supplies organized, as can hospitals and medical clinics. 5S can even be used in a communal kitchen to keep the fridge from filling up with expired food. It's really just a matter of determining what workspaces and work processes will benefit most from improved workplace organization.
5S Example
Look at the example below to see 5S in action. Before 5S, spaces are cluttered and confusing. After 5S, everything has an assigned place, which is often marked with floor marking tape, labels, and other visual cues.
When 5S is used in the workplace, it's easier to detect abnormalities and spot potential problems before they grow into significant issues.
The Costs of 5S vs. Long-Term Savings
Business leaders considering using 5S may wonder if 5S is expensive to implement. Generally, it's not. There may be an up-front investment in tools like floor marking tape and labels, and some time does need to be spent on training and on 5S activities, which takes up employees' time. In the long run, though, 5S makes processes run more smoothly and prevents mishaps, and those things usually save businesses money.